Film Casting Dryer / Disc Type Liquid Dryer
It is an indirect heated liquid contact dryer, energy-saving, low-cost, process-reducing, space-saving high-performance, high-efficiency liquid dryer, using indirect heat to dry materials by conduction, its principle is similar to the drum dryer or cylinder dryer used for papermaking, but instead of drying on the curved surface of the drum or cylinder, it dries the liquid on its two planes, and its installation area is only 40% of that of the drum dryer with the same drying surface area. Many powder manufacturers and companies that want to process or recycle resources or reduce the amount of wastewater are using this method.
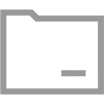
Product Attachments:
Keywords: Film Casting Dryer / Disc Type Liquid Dryer
- Description
- Schematic Diagram
- Parameter
- Result
-
Development prospects:
A large amount of wastewater and waste liquid containing recyclable resources are discarded due to the difficulty in handling. With the optical disc liquid dryer, the recovery of valuable resources in wastewater/waste liquid becomes easy and profitable.
Equipment introduction:
It is an indirect heated liquid contact dryer, energy-saving, low-cost, process-reducing, space-saving high-performance, high-efficiency liquid dryer, using indirect heat to dry materials by conduction, its principle is similar to the drum dryer or cylinder dryer used for papermaking, but instead of drying on the curved surface of the drum or cylinder, it dries the liquid on its two planes, and its installation area is only 40% of that of the drum dryer with the same drying surface area. Many powder manufacturers and companies that want to process or recycle resources or reduce the amount of wastewater are using this method.
Our optical disc surface drying makes it possible to dry various liquids, realizing a high-performance dryer with high efficiency, compactness and short process.
Widely used in ① In product manufacturing, pigments and other powders can be effectively extracted from product slurry; ② In terms of environmental protection, it can be used for various slurries, including post-processing of production by-products, such as rare metal recovery, food factory waste liquid treatment, oily waste liquid, salty waste water, and various factory waste liquid treatments.
Equipment features:
1、Large evaporation capacity: evaporation capacity of 20℃ water>200kg/m²·h
2、Good heat transfer coefficient: total heat transfer coefficient = 2300W/m²·k
3、High performance: The average production capacity per square meter of the dryer is twice that of the traditional drum dryer, while using lower steam pressure
4、Compact design: Since the dryer uses two sides of a thin plate for Drying, so the required floor area is about 40% of that required for a drum dryer
5、Energy saving/high efficiency: Due to the compact design, heat loss is reduced, up to 80%-85% thermal efficiency
6、Fast drying speed: The light weight of the heating device means that even large dryers can dry in 5 minutes
7、High quality products: Since the heating time is as short as 3-60s, it can reduce the exposure of product powder to high temperatures and damage
8、Short process: Since the liquid is directly dried and the residue is scraped into powder, the use of a disc dryer can save additional process steps such as concentration and crushing
9、Small footprint, low operating costs, simple operation, easy cleaning and maintenanceEquipment Application:
1. Suitable for a variety of applications, including powder production, waste liquid drying/concentration and recycling
2. Use one device to dry and crush all types of liquids (organic or inorganic), saving space and reducing installation costs
3. Dry waste liquid to reduce volume
4. Sell and profit from recycled resources such as precious metals or rare metals
5. Protect the global environment while reducing corporate costs -
Working principle:
1. Liquid is delivered to the disc surface
The original liquid in the circulation tank is pumped to the disc through the feed pipe. The liquid spreads into a thin film to improve heat transfer. The excess solution falls back into the circulation tank for re-feeding.2. Drying
As the disc rotates, the solution adhering to the surface of the heated disc is dried. By changing the disc speed and steam pressure (drying temperature), the processing capacity and moisture content of the dried product can be adjusted.
3. Collection of dried products
The scraper removes the product from the disc surface. The scraper continuously cleans the disc (heat transfer surface) to maintain good heat transfer. -
Equipment model
KC-1006
KC-1008
KC-1010
KC-1012
KC-1506
KC-1508
KC-1510
KC-1512
KC-1516
Disc diameter(mm)
1000
1500
Number of discs
6~12
6~16
Heat transfer area of each disk (㎡)
1.5
3.2
Total heat transfer area (㎡)
9-18
20-50
Overall dimensions
A
6100
6800
7500
8200
6100
6800
7500
8200
9600
B
4000
4000
4000
4000
4500
4500
4500
4500
4500
C
2200
2200
2200
2200
2800
2800
2800
2800
2800
-
Dryer drying process video:
Various types of wastewater/waste liquid Water Content (%WB)
Steam Pressure
(MPa)Liquid Processing Capacity
(kg/m²h)Amount of Dried Product
(kg/m²h)Original Liquid
Dried Product
Ceramics
67
0.2
0.3
100
33
Ferrite
60
0.1
0.3
175
70
Pigment
70
3.0
0.1
54
17
Beer Yeast
88
5.0
0.3
80
10
Liquid Distillation Residue
91
11.0
0.3
60
6
Milk Beverage (Waste)
89
1.2
0.15
29
3
Water-based Paint Waste water
98
10.0
0.13
63
1
Resist (Waste)
88
4.0
0.25
36
5
Concentrated Salt Water
80
10.0
0.25
48
11
Waste solution containing Oil
88
17.0
0.3
52
8
CAPACITIES FOR VARIOUS WASTE LIQUIDS Wastewater from/
Type of wastewaterWater Content of Original Liquid (W.B.) Water Content of Dried Product (W.B.) Drying Capacity(/㎡) Silicon Wafer 99.30% 34% 54kg/h Resist 88% 4% 36kg/h Cutting Oil 97.10% 4.70% 60kg/h Paint 95% 20% 43kg/h Polishing Agent 72% 0.50% 125kg/h Coolant 98% 54% 100kg/h Fodder 98% 3.50% 50kg/h Mold release Agent 97% 86% 99kg/h Fat 44% 7% 41kg/h Baby Wipe Production 99.30% 83% 73kg/h Cyanide-based 89% 7% 50kg/h Nitric Acid + HF Acid 82% 11% 50kg/h Wash water from Dust collector 90.40% 7.30% 97kg/h Distillation Residue from Waste Alcohol 92% 20% 50kg/h Fertilizer Factory 56.80% 7% 33kg/h Leachate 94.50% 3.40% 50kg/h RO Residue 92% 20% 50kg/h Water treatment facility 99.70% 4.50% 150kg/h Containing Ethanolamine 98% 67% 50kg/h Resin 55% 33% 97kg/h Photographic Processing 90% 8.40% 57kg/h Adhesive 96% 29% 57kg/h Food Processing 97% 8.20% 36kg/h
Your May Also Like
leave A Message
We will contact you as soon as possible